Category Archive: demolition
When it’s time to tear down an apartment building, the process isn’t as simple as swinging a wrecking ball and calling it a day. Apartment building demolition requires strategic planning, specialized equipment, and a strong focus on safety and environmental responsibility. At O’ROURKE, we have the experience and resources to handle complex demolition projects, including multi-story residential structures, with precision and care. Let’s walk through the key steps and considerations involved in demolishing an apartment building, and why working with an experienced demolition team makes all the difference.
Why Apartment Building Demolition Is More Complex Than It Looks
Apartment buildings are different from single-family homes or smaller structures. They’re typically larger, taller, and constructed from a combination of materials like concrete, steel, and brick. Plus, they often sit in densely populated areas, making logistics and safety even more critical.
Demolishing an apartment building involves:
- Managing utility shutoffs and disconnections
- Environmental testing for hazardous materials like asbestos and lead
- Coordinating with city officials for permits and traffic control
- Protecting nearby structures and minimizing dust and noise
- Managing waste disposal and recycling
This isn’t a job for just any demolition crew, it requires a highly trained team with specialized equipment and an understanding of complex building systems.
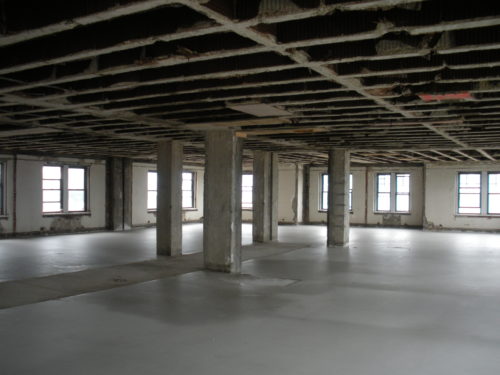
The Steps to Successful Apartment Building Demolition
Site Assessment and Planning
Before any demolition starts, O’ROURKE conducts a thorough site assessment. This includes evaluating the building’s structure, identifying hazardous materials, and mapping out the safest approach for demolition. We’ll also work with local authorities to secure the necessary permits and create a plan for traffic control and pedestrian safety.
Example: If the building contains asbestos, it must be professionally removed following EPA guidelines before demolition can proceed.
Hazardous Material Abatement
Older apartment buildings often contain hazardous materials like asbestos, lead-based paint, and mold. Our certified abatement team removes these materials safely and disposes of them according to federal, state, and local regulations. This step is essential for protecting workers and the surrounding community.
Structural Demolition
Once the site is cleared and prepped, the actual demolition begins. At O’ROURKE, we tailor our approach based on the building’s structure, location, and environmental factors. Depending on the size and location of the building, we may use one of several methods:
- Mechanical Demolition: Excavators, bulldozers, and other heavy equipment are used to tear down the building piece by piece.
- Implosion: Controlled explosives are used to bring down large structures quickly and safely. This is more common for taller apartment complexes.
- Deconstruction: In some cases, we’ll carefully dismantle parts of the building to salvage materials like wood, metal, and concrete for recycling.
Debris Removal and Recycling
Demolition generates a lot of debris, but not all of it goes to the landfill. We recycle as much material as possible, including concrete, steel, and wood. Our goal is to minimize environmental impact and reduce waste.
Example: Concrete from a demolished building can be crushed and reused as a base for new construction projects.
Site Cleanup and Preparation
After the building is down and the debris is removed, we handle site grading and leveling. If the property is being redeveloped, we’ll prepare the site for new construction. We make sure the site is clean, stable, and ready for the next phase of development.
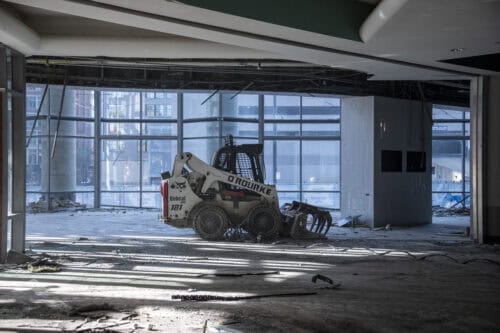
Common Challenges in Apartment Building Demolition (and How We Solve Them)
Tight Urban Spaces
In urban environments, apartment buildings are often surrounded by other structures, making demolition tricky. O’ROURKE uses precise equipment and controlled methods to prevent damage to neighboring properties.
Noise and Dust Control
Demolition can be noisy and dusty, but we take steps to minimize disruption. We use water sprays to control dust and schedule demolition work during off-peak hours when possible.
Traffic and Pedestrian Safety
We work closely with city officials to reroute traffic and establish safe pedestrian zones. Our team sets up barriers and signage to keep everyone safe.
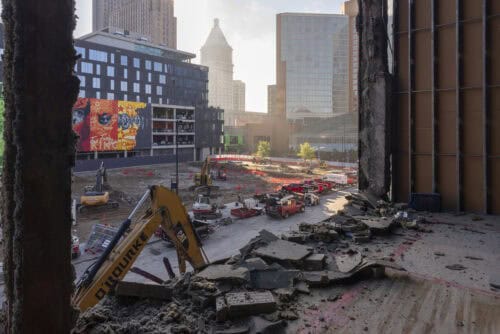
Why Choose O’ROURKE for Apartment Building Demolition?
- Experience: We’ve handled apartment building demolitions of all sizes, from small complexes to high-rise towers.
- Safety First: We follow strict safety protocols to protect workers, neighbors, and the surrounding environment.
- Environmental Responsibility: We prioritize recycling and sustainable practices to minimize waste.
- Advanced Equipment: Our fleet includes high-reach excavators, hydraulic shears, and other specialized machinery.
- Full-Service Approach: From site prep to cleanup, we manage the entire process.
Ready to Get Started?
Apartment building demolition requires a professional approach, and O’ROURKE delivers. Whether it’s a small residential complex or a multi-story high-rise, we have the experience and equipment to handle the job efficiently and safely.
Affordable Housing Demolition: Safe, Efficient, and Responsible Solutions
Affordable housing plays a critical role in communities by providing stable and cost-effective living options for families and individuals. However, when these structures become unsafe, outdated, or are slated for redevelopment, demolition becomes a necessary step toward revitalizing the area. At O’ROURKE, we specialize in safe, efficient, and environmentally responsible affordable housing demolition services, helping communities make way for modern, sustainable housing while maintaining a commitment to safety and compliance.
Why Affordable Housing Demolition Is Necessary
Affordable housing projects often have long lifespans, but like any structure, they eventually face wear and tear that can make them unsafe or unsuitable for modern living. Here are some common reasons for affordable housing demolition:
Structural Instability
Over time, affordable housing complexes may suffer from foundational issues, water damage, or aging materials that make them structurally unsound. When repairs are no longer viable or cost-effective, demolition allows for a fresh start.
Asbestos and Hazardous Materials
Many older affordable housing buildings were constructed with materials like asbestos, lead paint, and outdated insulation that pose health risks. Safe demolition and proper hazardous material removal are essential to protecting public health and ensuring future construction meets modern safety standards.
Urban Redevelopment and Modernization
Cities and developers may seek to revitalize neighborhoods by replacing aging affordable housing with modern, energy-efficient structures. Demolition clears the way for redevelopment, improving the overall quality of housing and infrastructure.
Compliance with Updated Building Codes
Affordable housing built decades ago may no longer comply with current affordable housing codes. Rather than attempting expensive retrofits, complete demolition and reconstruction can be a more cost-effective and long-term solution.
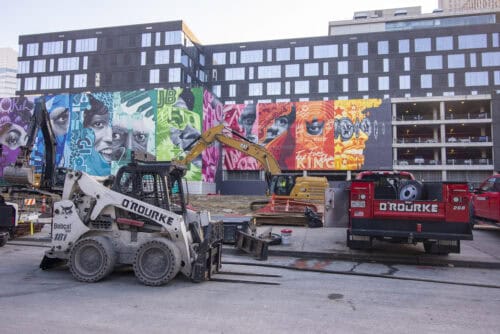
O’ROURKE’s Approach to Affordable Housing Demolition
At O’ROURKE, we understand that affordable housing demolition requires a strategic and thoughtful approach. Our team brings decades of experience, advanced equipment, and a focus on environmental responsibility to every project.
Comprehensive Planning and Permitting
Affordable housing demolition often involves working closely with local governments, housing authorities, and community stakeholders. O’ROURKE handles all permitting, planning, and pre-demolition assessments to ensure compliance with regulations and minimize disruptions to the surrounding community.
Safe and Efficient Demolition Techniques
Our team uses industry-leading equipment and techniques to execute demolition projects efficiently while maintaining strict safety protocols. This includes:
- Controlled demolition to minimize dust and noise.
- Structural assessments to determine the safest demolition approach.
- Protective barriers to safeguard neighboring properties and public spaces.
Hazardous Material Removal and Abatement
Affordable housing built before the 1980s often contains hazardous materials like asbestos, lead, and mold. O’ROURKE’s certified abatement specialists carefully identify and remove these materials before demolition begins, ensuring the safety of workers and the surrounding community.
Environmental Responsibility and Recycling
We are committed to minimizing environmental impact during demolition. This includes:
- Recycling concrete, metal, and other reusable materials.
- Proper disposal of hazardous waste in compliance with EPA guidelines.
- Dust and emissions control to protect air quality.
Site Cleanup and Preparation
After demolition is complete, O’ROURKE handles all site cleanup and preparation for future construction. This includes grading the land, removing debris, and ensuring the site is ready for redevelopment.
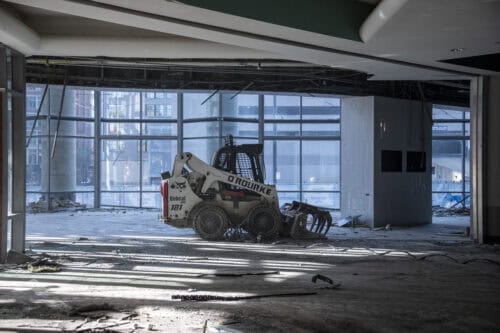
Challenges in Affordable Housing Demolition
Affordable housing demolition comes with unique challenges that require expertise and adaptability:
- Community Impact: Displacing residents and removing long-standing housing structures can create social and economic tension. We work closely with housing authorities and developers to ensure a smooth transition and minimize disruptions.
- Historical Preservation: Some affordable housing complexes may have historical significance. O’ROURKE evaluates each project’s historical value and works with preservation groups when necessary.
- Budget Constraints: Affordable housing projects often operate under tight budgets. O’ROURKE delivers cost-effective demolition solutions without compromising on safety or quality.
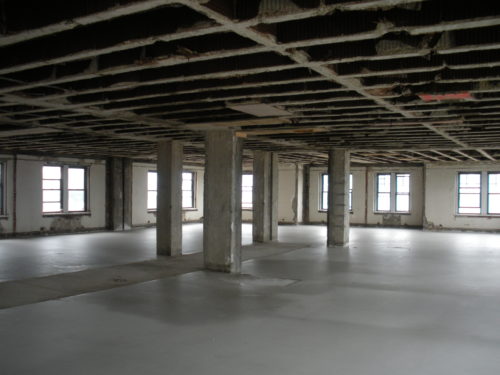
Why Choose O’ROURKE for Affordable Housing Demolition
O’ROURKE is a trusted leader in the demolition industry with a proven track record of handling complex affordable housing projects. Our team understands the importance of balancing efficiency, safety, and environmental responsibility. By partnering with O’ROURKE, developers and housing authorities can expect:
- Expert project management from start to finish.
- Strict compliance with all local, state, and federal regulations.
- Transparent pricing and detailed project timelines.
- A focus on community engagement and minimizing disruption.
Ready to Get Started?
Affordable housing demolition is a critical step toward improving community infrastructure and creating modern, safe, and accessible housing options. O’ROURKE has the expertise and resources to handle affordable housing demolition projects of any size and complexity.
Data center demolition and renovation are essential to keeping up with the rapid pace of technology and meeting the ever-growing demands of modern businesses. Modernizing data centers isn’t just a trend; it’s a necessity. Outdated facilities often consume excessive energy, offer inadequate capacity, and struggle to maintain data security.
Why O’ROURKE is the Trusted Partner for Complex Projects
As technology evolves at lightning speed, data centers must keep pace. Whether your facility is outdated, inefficient, or simply at capacity, demolition and renovation are critical steps in modernizing infrastructure to meet today’s business demands.
At O’ROURKE, we specialize in high-stakes demolition and renovation for mission-critical environments—especially data centers. These aren’t typical construction jobs. They demand precision, speed, and a deep understanding of the systems that keep businesses running.
Why Modernize Your Data Center?
- Boost Efficiency: Newer systems reduce energy use and operating costs.
- Strengthen Security: Older facilities often lack safeguards against modern cyber threats.
- Increase Reliability: Minimize downtime with upgraded infrastructure built for today’s demands.
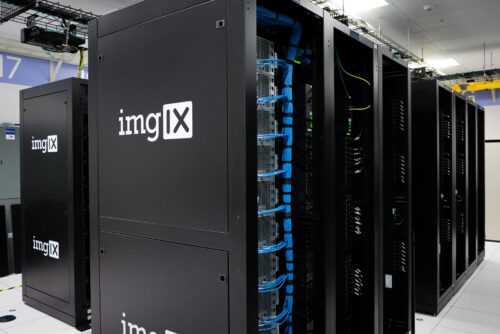
Our Approach: Strategic, Safe, and Sustainable
Successful data center demolition starts long before the first wall comes down. It requires strategic planning, expert execution, and strict adherence to safety and environmental regulations. Diving headfirst into demolition or renovation without preparation can lead to unexpected costs, delays, or even catastrophic failures. O’ROURKE works closely with clients during the planning phase to identify their unique goals and create a roadmap tailored to their needs. Our detailed assessments and collaborative approach ensure no detail is overlooked.
Comprehensive Site Assessment
Evaluate structural integrity, environmental hazards, and reuse potential.
Customized Project Planning
Define goals—whether a full teardown or partial upgrade—and set a clear timeline.
Budget Optimization
Account for permits, labor, materials recycling, and disposal—without surprises.
Sensitive Systems Management
Safely decommission servers, electrical systems, and data infrastructure.
Responsible Demolition with Maximum Recovery
When it comes to tearing down or revamping a data center, waste is inevitable. But that doesn’t mean it all has to end up in a landfill. Data centers house valuable materials—from server racks to copper cabling. We prioritize recycling, material recovery, and eco-friendly disposal:
- E-Waste & Electronics Recycling
- Salvage of Metals & Equipment
- Proper Handling of Asbestos, Lead & Batteries
- Site Remediation & Restoration Planning
Navigating the Challenges of Data Center Demolition
- Complex Equipment Removal Without Disruption
- Hazardous Material Mitigation
- Maintaining Site Security and data integrity throughout the project
Addressing Environmental Concerns
The environmental impact of demolition often flies under the radar, but it shouldn’t. Data centers contain materials that can be recycled, repurposed, or safely disposed of to minimize waste.
- E-Waste Recycling: Servers, cables, and other electronics shouldn’t end up in a landfill.
- Sustainable Practices: Look for opportunities to salvage usable materials or reduce the project’s carbon footprint.
- Energy-Efficient Materials: Using reflective roofing, insulated walls, and energy-efficient windows to lower energy consumption.
- LEED Certification: Achieving Leadership in Energy and Environmental Design (LEED) status as a benchmark of sustainability.
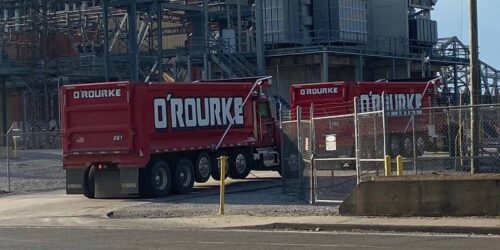
Why Hire O’ROURKE As Your Demo Contractor?
As a leading demolition contractor trusted by data-driven businesses across the country, O’ROURKE delivers:
✔ Expert teams familiar with high-security and mission-critical environments
✔ Transparent communication and proactive problem-solving
✔ Environmental compliance and zero-tolerance safety culture
At O’ROURKE, we’re experts in addressing these challenges. Our team employs cutting-edge tools and methods to ensure every demolition project is safe, secure, and environmentally responsible.
Looking to Modernize Your Data Center?
Whether you’re demolishing an outdated facility or prepping for renovation, trust O’ROURKE to deliver results that are on time, on budget, and aligned with your goals?
When it comes to updating your property or repurposing an office space, the idea of gutting an old office building might seem overwhelming. But it doesn’t have to be a hassle if you choose the right demolition contractors. At O’ROURKE, we specialize in office demolition services that property owners like you can count on to get your job done right and within budget.
What is Office Demolition?
Office demolition is the process of tearing down or dismantling office spaces, either partially or completely. Maybe the layout isn’t working anymore. Maybe the building is old, unsafe, or just in the way of something bigger and better. That’s where office demolition comes in. It’s a structured, strategic process that involves planning, permitting, and precision work to ensure safety and efficiency.
There are two main types of office demolition:
Partial office demolition – This is common when companies want to renovate or repurpose their space. It might involve removing walls, ceilings, fixtures, or flooring while keeping the structure intact.
Full office demolition – This means taking the entire building down to the foundation. It’s necessary when an office building is beyond repair or a new structure is planned for the site.
Regardless of the scope, the process requires expertise, the right equipment, and strict safety measures to prevent damage to surrounding properties and ensure environmental compliance.
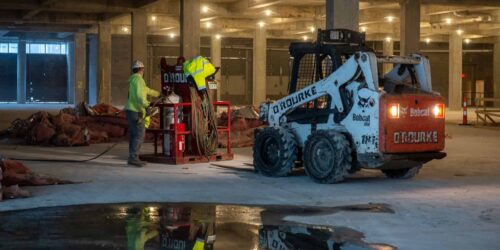
Office Demolition Methods and Techniques
Office demolition isn’t a one-size-fits-all process. Different projects require different methods. Here are the most common techniques used in commercial office demolition:
Interior Strip-Outs for Office Renovation
Not all office demolition projects mean tearing down an entire building. Many businesses choose interior demolition, which involves removing non-structural elements while keeping the building’s framework intact. Interior demolition is ideal for companies redesigning office workspaces or upgrading infrastructure without starting from scratch.
- Walls, partitions, and ceilings – Breaking down outdated layouts
- Flooring and fixtures – Removing worn-out materials
- Electrical and plumbing systems – Prepping for upgrades
Understanding the Demolition Process
Office demolition isn’t just about knocking down walls; it’s a detailed process that demands expertise and planning. Whether you’re clearing space for a new development or repurposing an existing site, professional demolition ensures the job is done right. Here’s a quick rundown of what you can expect:
1) Assessment and Planning – Experts conduct detailed inspections, evaluating the structure and identifying potential hazards. A thorough assessment prevents unexpected hazards that could delay the project or create environmental and safety risks.
2) Preparation – Before any heavy machinery gets involved, the site is prepped. This might include disconnecting utilities, securing permits, and marking out safe zones.
3) Execution – With a clear plan in place, demolition specialists use specialized equipment to dismantle the building safely.
4) Debris Removal – During the removal process, we sort debris into categories—metals, concrete, wood, and hazardous materials—to streamline recycling and recovery efforts.
5) Cleanup – Once the structure is down, the final phase involves debris removal and recycling where possible.
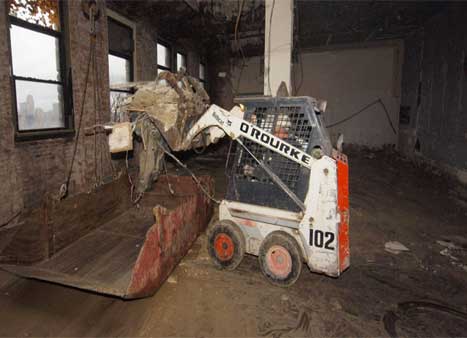
Signs Your Office Needs Demolition
Demolition isn’t always the first option. Sometimes, a renovation or retrofit might be enough to bring an office up to modern standards. But there are clear signs that an office building is beyond saving:
- Structural Damage – Cracks in walls, sagging ceilings, and uneven floors aren’t just cosmetic issues. They can signal serious foundation problems that make a building unsafe.
- Outdated Infrastructure – Some older office buildings have electrical, plumbing, and HVAC systems that are too costly to update. If repairs outweigh replacement costs, demolition makes more sense.
- Asbestos or Hazardous Materials – Buildings from past decades often contain asbestos, lead paint, or other hazardous materials that require careful removal. In some cases, full demolition is the best way to safely remove these risks.
- New Construction Needs – Sometimes, it’s just about progress. Whether it’s expanding a business, replacing an outdated structure, or repurposing land for a different use, demolition makes room for what’s next.
Environmental and Safety Considerations
Office buildings, especially older ones, can contain hazardous materials that require careful handling. Rushing into demolition without proper environmental assessments can lead to serious health risks, legal issues, and expensive cleanups.
Some of the most common environmental concerns during office demolition include:
- Asbestos – Frequently found in insulation, ceiling tiles, and old flooring. Inhaling asbestos fibers can cause severe lung diseases.
- Lead-Based Paint – Many pre-1978 buildings contain lead paint, which requires special removal procedures to prevent contamination.
- Mold and Biological Hazards – Water-damaged buildings often harbor mold, which can trigger respiratory issues if not properly handled.
- Underground Storage Tanks (USTs) – If an office building has an old fuel tank on-site, it must be safely removed to prevent soil contamination.
A professional demolition company assesses and mitigates these risks, ensuring that hazardous materials are safely removed before demolition begins. Comprehensive safety measures are in place to protect everyone on-site, from demolition workers to neighboring residents.
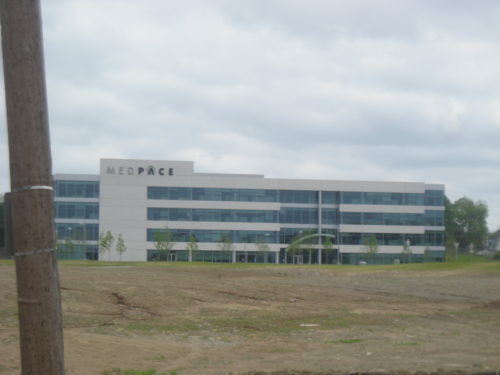
The Benefits of Choosing O’ROURKE
At O’ROURKE, we’re not just about taking down buildings, we’re about building trust with our clients through exceptional service and sustainable practices. When you choose us, you’re choosing a partner committed to quality, safety, and the environment.
Expertise and Experience
Our team brings 60+ years of experience to every project. We’re proud of our track record, which includes numerous successful office demolitions. Our crew is trained, certified, and experienced in handling the complexities of office demolition. We use the latest machinery designed specifically for efficient and safe demolition. Our approach is both systematic and innovative, ensuring that every office demolition project is executed with precision.
Costs Involved in Office Demolition
One of the first questions property owners ask is: how much will this cost? The price of office demolition varies widely depending on several key factors:
- Building Size & Type – A multi-story office building costs more to demolish than a single-floor space due to structural complexity.
- Materials & Hazardous Substances – Asbestos removal, lead paint mitigation, or specialized waste disposal can add to costs.
- Demolition Method – Selective demolition (preserving certain structures) costs more than full-service demolition projects
- Site Conditions – Urban environments may require extra safety measures to protect nearby buildings, increasing labor and permit costs.
- Waste Management & Cleanup – The cost of hauling debris away and ensuring environmental compliance is factored into the total price.
To get an accurate estimate, property owners should request a detailed quote from O’ROURKE that breaks down costs by labor, equipment, permits, and disposal fees. No two projects are alike, so prices for office demolition can range from $10,000 to $500,000+ depending on complexity.
Get a Quote for Your Office Demolition Project
Ready to take the next step? Whether you need a partial interior demolition or a full office teardown, O’ROURKE has you covered. Contact us today for a free estimate.
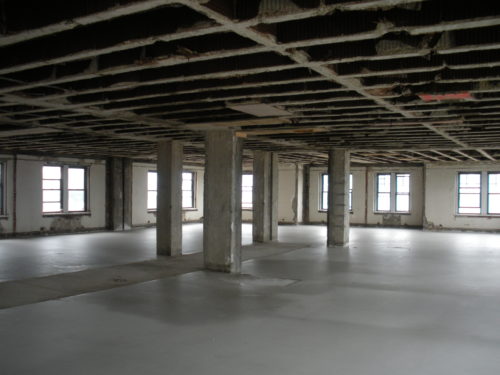
Frequently Asked Questions (FAQs)
Here are some of the most common queries property owners have about office demolition services, along with straightforward answers.
How long does an office demolition project typically take?
The duration of a demolition project varies based on the building’s size, complexity, and site conditions. While smaller projects might wrap up in a matter of days, larger or more complex demolitions can extend over several weeks. At O’ROURKE, we work hard to provide a realistic timeline and keep you updated throughout the process.
How do you handle hazardous materials like asbestos?
Safety is our top priority. Our team is trained in the safe handling and disposal of hazardous materials. We work in compliance with all regulatory requirements, using specialized equipment to remove and dispose of materials like asbestos and lead safely.
What measures are in place to protect surrounding properties?
Protecting neighboring properties is a key part of our safety protocol. We establish secure perimeters, use dust suppression methods, and coordinate with local authorities to ensure that the demolition does not adversely affect nearby structures or residents.
Can materials from the demolition be recycled or repurposed?
Absolutely. One of our core practices is to maximize recycling and repurposing of materials. We sort debris into recyclables and work with local recycling firms to ensure that as little material as possible ends up in landfills. This not only supports environmental sustainability but can also reduce disposal costs.
What if there are unexpected complications during the demolition?
Every project carries its own set of challenges. However, our team is prepared to handle unforeseen issues swiftly and effectively. Clear communication, detailed planning, and on-site expertise help us address any hiccups promptly, ensuring the project stays on track.
You’ve got a property with potential—great location, lots of space—but it’s a brownfield site. Maybe it’s a shuttered factory, a former gas station, or even an old dry cleaner’s shop. You know cleaning it up is the key to unlocking its value, but where do you even start?
While brownfield land can pose health and environmental risks, these properties offer incredible redevelopment opportunities when properly remediated. O’ROURKE specializes in transforming these brownfield sites into safe, usable spaces. Our team takes a customized approach to each project, addressing unique site challenges with precision and care.
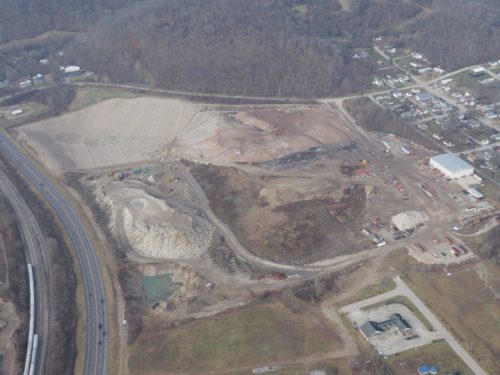
What Are Brownfield Sites?
The EPA defines brownfields as real estate where the presence (or potential presence) of hazardous substances, pollutants, or contaminants complicates redevelopment. But don’t let that scare you—brownfield sites aren’t hopeless. In fact, with the O’ROURKE’s remediation approach, they can be turned into the ideal real estate development location.
Brownfields are real estate with baggage. These are properties where past industrial or commercial use has left behind contamination. It’s not just old factories; brownfields can include abandoned gas stations, vacant warehouses, and even properties used for manufacturing.
Why Brownfield Clean-Up Matters
An abandoned property sitting idle doesn’t just hurt its owner—it can drag down entire neighborhoods. Contaminants from brownfields can seep into groundwater, pollute the air, and damage ecosystems. But with professional remediation, these hazards can be mitigated. Cleaning up brownfields can even act as a spark for economic growth. For example:
- Property value increases: Remediation removes the stigma of contamination, making the site more valuable.
- Tax incentives: Programs like the EPA’s Brownfields Program offer grants, tax breaks, and funding assistance for clean-up projects. These incentives reduce costs and make redevelopment more appealing.
- New businesses thrive: Clean sites attract tenants and developers, bringing jobs and revenue to the area.
With O’Rourke by your side, you can turn environmental challenges into opportunities for growth. Whether you’re a private property owner, a developer, or a municipality, O’ROURKE’s team of experts is ready to guide you through every step of the brownfield remediation process.
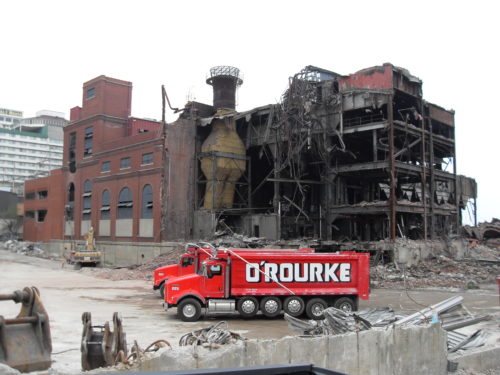
Understanding the EPA’s Role & Brownfield Funding
The EPA Brownfields Program is a cornerstone of the remediation process. Its mission is to empower communities and property owners to tackle contaminated sites without breaking the bank.
Through this program, the EPA offers:
- Grants for Assessments and Clean-Ups: These help cover costs for site evaluations and remediation.
- Technical Assistance: Expert guidance ensures that property owners navigate complex environmental regulations.
- Redevelopment Incentives: These include liability protection and tax breaks, encouraging the reuse of previously contaminated land.
The program’s support can be a game-changer, especially for smaller projects.
How O’ROURKE Handles Brownfield Remediation
At O’ROURKE, brownfield remediation isn’t just another project—it’s a mission to transform neglected spaces into thriving properties. With six decades of experience in the demolition and environmental industry, we have developed a reputation for delivering comprehensive, tailored solutions for even the most challenging sites. Here’s how we handle brownfield remediation:
Thorough Site Assessments and Planning
O’ROURKE begins every project with a meticulous environmental site assessment. Using advanced tools like ground-penetrating radar, soil sampling equipment, and aerial surveys, we leave no stone unturned.
Before you break ground on the clean-up, you need to know what you’re dealing with. This is where environmental site assessments (ESA) come in. There are two main phases:
- Phase I ESA: A historical review of the property to identify potential contamination risks. It’s real estate detective work—digging through old records, maps, and permits.
- Phase II ESA: Hands-on testing, including soil and water sampling, to confirm the presence of contaminants. Tools like ground-penetrating radar and soil analysis kits help our experts pinpoint problem areas. The goal is to get a clear picture of what’s lurking beneath the surface.
From there, we develop a remediation plan that aligns with the site’s unique needs and regulatory requirements.
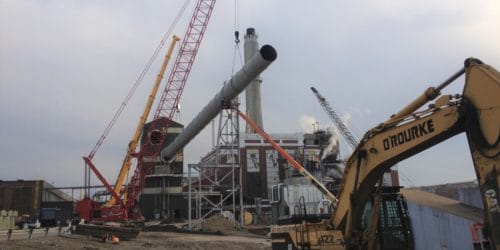
Developing a Remediation Plan
Once the assessment is complete, it’s time to map out your remediation strategy. This isn’t a one-size-fits-all process. The plan should consider costs, safety protocols, and regulatory requirements. O’ROURKE regularly collaborates with the EPA and local environmental agencies to streamline approvals and ensure compliance.
Cutting-Edge Environmental Cleanup Techniques
O’Rourke employs the latest technology and techniques for brownfield cleanup. Many brownfield sites require partial or full demolition of existing structures. Demolition isn’t just about knocking down buildings, it’s about doing it safely and responsibly, especially when contaminants are present.
Once the structures are down, the next challenge is managing the cleanup of debris and waste. Some materials, like concrete or metal, can be recycled, while others require special handling. We specialize in handling asbestos, lead, and other hazardous materials that may be present in existing structures, ensuring a seamless transition from demolition to remediation.
End-to-End Project Management
Navigating regulations can feel like walking through a maze, but it’s an essential part of the process. Brownfield projects are closely monitored by agencies like the EPA, which ensures clean-up efforts meet strict standards.
From securing necessary permits to coordinating with regulatory agencies, O’Rourke takes care of the paperwork and logistics so you don’t have to. We maintain clear communication with our clients throughout the process, providing updates and addressing concerns promptly. Our team ensures every project stays on schedule and within budget.
Commitment to Safety and Compliance
Safety is at the heart of every project we undertake. Our crews are trained in handling hazardous materials and adhere to strict safety protocols. O’Rourke also ensures full compliance with federal, state, and local regulations, giving clients peace of mind that the project meets all legal requirements.
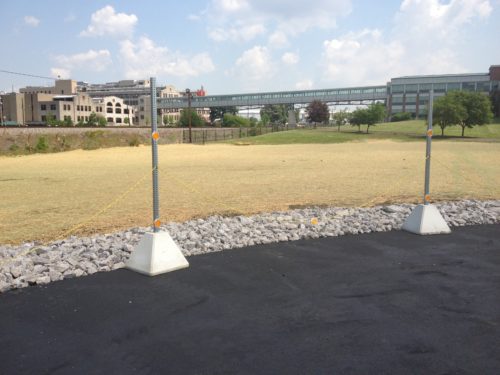
Transforming Brownfields For Redevelopment
Taking on a brownfield project might feel daunting, but the payoff is worth it. Cleaning up contaminated sites not only protects the environment and public health but also opens the door to economic opportunities for redevelopment. By working with experienced professionals, navigating regulations, and tapping into available funding programs, you can turn your property into a safe, valuable asset.
So, what’s stopping you? Reach out to O’ROURKE today and take the first step toward transforming your brownfield site into something truly remarkable.
Demolishing a building is no small task. But when that building has post-tensioned concrete, the stakes get even higher. Their demolition demands a level of precision and expertise that most contractors aren’t equipped to handle.
If you’re a property owner planning a large demolition project, you need to be aware because improper handling can lead to serious safety hazards, skyrocketing costs, and unexpected delays.
In this helpful guide, we’ll break down what makes post-tensioned concrete unique, why it requires specialized demolition techniques, why O’ROURKE is the right partner for your demo project.
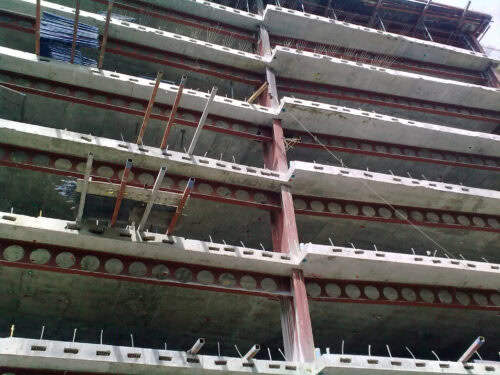
What Is Post-Tensioned Concrete?
Post-tensioning is a construction technique where steel cables, also called tendons, are embedded in concrete and then stretched tight after the concrete has hardened. This process creates compressive forces, allowing the structure to withstand heavy loads or span greater distances without the bulk of traditional reinforced concrete.
So, why was post-tensioning so popular? In its peak during the 1960s, it was a cost-effective solution for creating durable, lightweight structures. The reduced weight made construction faster and cheaper, while the added strength allowed for innovative designs.
However, its popularity declined as new materials and construction methods emerged. Today, post-tensioned structures still exist, but many are reaching the end of their lifespan. This means they’re often prime candidates for demolition—and O’ROURKE has the expertise to handle these projects with the care they demand.
Key Features of Post-Tensioned Concrete
What makes post-tensioned concrete so unique? It’s all about those tensioned cables. Imagine a rubber band stretched to its limit and held in place—that’s the essence of post-tensioning. This method distributes stress more evenly throughout the concrete, reducing cracks and making the structure more durable over time.
However, those same cables can pose a challenge when it comes to demolition. They store a tremendous amount of energy, which can release unpredictably if not handled correctly. This isn’t something you’d want to approach without proper training or tools. It’s a double-edged sword: what makes the material strong during construction becomes a potential hazard during demolition.

Structures with Post-Tensioned Concrete
You’ve likely encountered post-tensioned concrete without realizing it.
- Parking Garages: Lightweight slabs made it easier to create multiple levels without the need for excessive support columns.
- High-Rise Buildings: The combination of strength and reduced weight allowed for slimmer, taller designs.
- Bridges: Long spans over rivers or highways often relied on post-tensioning to achieve their length.
- Stadiums: The massive beams and supports in sports arenas often use this method for stability and flexibility.
At O’ROURKE, we’ve worked with all types of post-tensioned systems, giving us a deep understanding of the unique challenges they present. Parking garages may have hidden cables that pose safety risks, while bridges might require precise sequencing to avoid catastrophic collapses.
The Challenges of Demolishing a Post-Tensioned Structure
Demolishing post-tensioned concrete isn’t just about brute force. The internal steel tendons—designed to be under extreme tension—make the process significantly more complicated.
Imagine cutting through a post-tensioned slab without knowing where the tendons are. The sudden release of tension could cause the steel to snap violently, sending shards of concrete and metal flying. This isn’t just a theoretical risk; it’s a genuine hazard that puts workers and nearby properties at risk.
Additionally, post-tensioned demolition must account for:
- Unpredictable Behavior: Tendons can behave erratically when their tension is released improperly.
- Structural Dependencies: Cutting the wrong section can lead to unintended collapses elsewhere.
- Public Safety: Demolitions in urban areas need extra precautions to protect pedestrians and adjacent buildings.
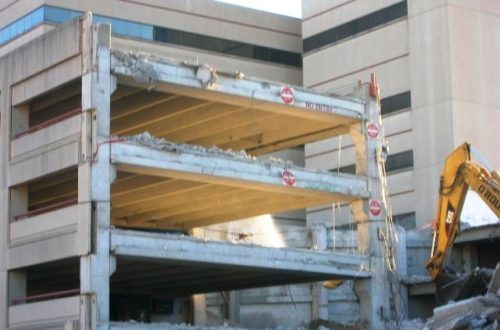
Why Specialized Demo Techniques Are Necessary
If you’ve ever seen a traditional concrete structure demolished, you might think it’s a straightforward process. Wrecking balls, excavators, or even explosives can reduce a reinforced concrete building to rubble in hours. But with post-tensioned concrete, it’s not that simple.
- Controlled Release of Tension: You can’t just cut into a post-tensioned beam or slab. The tension in the tendons must be carefully released to prevent dangerous snaps.
- Precision Demolition: Tools like concrete saws and hydraulic breakers are often needed to dismantle sections piece by piece.
- Avoiding Chain Reactions: Improper demolition could destabilize the entire structure, leading to uncontrolled collapses.
- Environmental Hazards: Dust, debris, and potential contamination from corroded tendons require strict management protocols.
This is why hiring O’ROURKE’s demolition experts is critical. Our team has the experience in post-tensioned demolition to know how to approach each structure methodically, prioritizing safety and efficiency.
Health and Safety Considerations
Safety isn’t just a box to check—it’s the cornerstone of every post-tensioned demolition project. From the first assessment to the final piece of debris, precautions must be built into every step of the process.
- Comprehensive Assessments: Every structure is different. Mapping the location of tendons and assessing their condition is critical before any work begins.
- Worker Training: Teams need specialized training to understand how post-tensioning systems work and how to dismantle them safely.
- Protective Equipment: Safety gear like helmets, gloves, and protective shields are mandatory, especially when working with heavy machinery or explosives.
- Compliance with Regulations: Adhering to OSHA and local guidelines isn’t optional—it’s the baseline for safe operations.
Ultimately, safety is about more than protecting workers. It’s about ensuring the project runs smoothly, without accidents or costly setbacks.
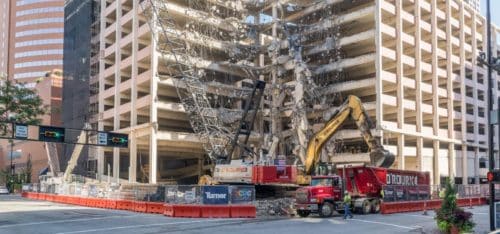
Methods of Post-Tensioned Demolition
When it comes to post-tensioned demolition, the method matters. Each structure demands a customized approach, and at O’ROURKE, we tailor our techniques to the specific needs of your project.
Controlled De-tensioning
De-tensioning is the cornerstone of safe post-tensioned demolition. Think of it as carefully disarming a loaded spring. Our team meticulously identifies and releases the tension in steel tendons, section by section.
Mechanical Demolition
For structures that can accomodate heavy machinery, mechanical demolition can be highly effective. Mechanical methods are often used in tandem with de-tensioning to ensure safety and efficiency. Our operators are highly trained to handle these tools with pinpoint accuracy, reducing the risk of unintended damage.
Explosive Demolition
While less common, explosive demolition can be an effective option for certain post-tensioned structures, such as large bridges or stadiums.
O’ROURKE’s Expertise in Post-Tensioned Demolition
At O’ROURKE, our team is made up of seasoned professionals who understand the complexities of post-tensioned structures. From engineers to equipment operators, every member of our team plays a critical role in ensuring the project’s success.
We also invest heavily in ongoing training, ensuring that our crew stays up-to-date on the latest techniques and safety protocols. This dedication to expertise is one of the many reasons why property owners trust O’ROURKE with their most challenging demolition projects.
Request a Consultation Today
Every successful post-tensioned demolition starts with a solid plan. At O’ROURKE, we leave nothing to chance. From the initial assessment to the final debris removal, our process is rooted in meticulous preparation. Ready to get started? Contact O’ROURKE to schedule a consultation.
Demolishing commercial buildings requires careful planning, professional expertise, and a clear understanding of associated costs. Whether you’re looking to replace an outdated structure or repurpose a site, understanding commercial demolition costs ensures your project stays within budget while meeting regulatory standards. This guide provides a detailed overview of the factors influencing commercial demolition costs and what you need to know to hire the right contractor.
The Average Cost per Square Foot to Demolish Commercial Buildings
The average cost to demolish a commercial building ranges from $4 to $8 per square foot, depending on the project scope, materials used in the structure, and location. However, for high-rise buildings or projects requiring specialized equipment, costs may exceed $10 per square foot. These averages include labor, equipment, and debris removal but exclude additional factors like environmental remediation.
Commercial Interior Demolition Costs
Interior demolition costs differ significantly from full-scale structural demolition. For commercial spaces, the average price ranges from $2 to $6 per square foot. This type of demolition involves removing non-structural elements such as walls, flooring, or ceilings to prepare a space for renovation. The price depends on factors like the materials being removed, accessibility, and whether hazardous materials like asbestos or lead are present.
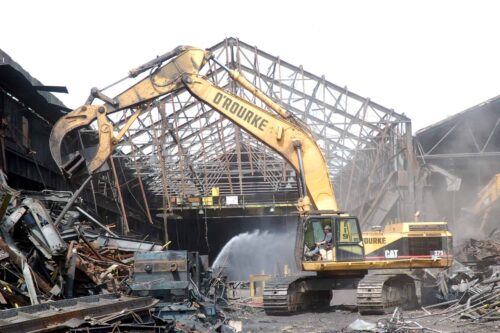
Factors That Affect Commercial Demolition Pricing
Several factors influence the cost of commercial demolition. Understanding these variables can help you anticipate and manage expenses effectively.
Building Type
The type of building—whether a warehouse, office complex, or industrial facility—affects costs. More robust structures, such as factories, may require heavy-duty equipment and specialized crews, increasing expenses. In contrast, simpler buildings, like small office spaces, typically involve less-intensive processes.
Different building types require varied approaches to demolition. A steel-framed office building may necessitate heavy machinery and precise dismantling, while a concrete warehouse may involve more labor-intensive methods. Each type demands unique expertise and equipment, influencing the final cost.
Remediation & Environmental Concerns
Environmental remediation, such as asbestos or lead paint removal, significantly impacts demolition costs. If hazardous materials are detected, specialized contractors must handle their safe removal, which can add $2 to $4 per square foot to the overall budget.
Building Size
Larger buildings often benefit from economies of scale, reducing the per-square-foot cost. However, the total cost will still increase with size due to the extended timeline, additional labor, and larger volume of debris. For example:
- A small 5,000-square-foot structure might cost $30,000 to $50,000.
- A large 50,000-square-foot facility could range from $200,000 to $400,000.
Ease of Access & Surrounding Area
Accessibility plays a critical role in pricing. If the building is located in a dense urban area, contractors may face challenges like limited equipment maneuverability, noise restrictions, and safety precautions for surrounding structures. These complexities can add 10-20% to the base cost.
Geographic Location
Labor rates, disposal fees, and material recycling availability vary by location. For instance, urban centers tend to have higher costs due to stricter regulations and higher wages, while rural areas may benefit from reduced expenses. O’ROURKE Wrecking Company regularly completes commercial demolition projects throughout the United States, with many demolition projects completed in Cincinnati, Columbus, Nashville, and beyond.
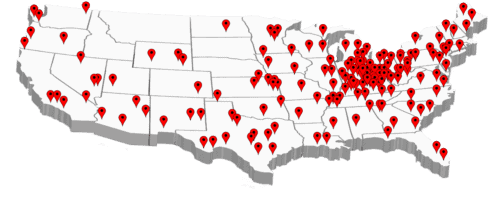
Additional Costs to Consider Besides the Demolition Itself
Demolition projects often come with ancillary costs beyond the physical teardown of a building. These are critical for planning an accurate budget:
Asbestos & Environmental Remediation
Asbestos is commonly found in older buildings, and its safe removal is a legal requirement before demolition. Handling asbestos remediation, lead paint removal, or other hazardous materials requires specialized contractors. Depending on the extent of remediation needed, the cost can significantly increase the total project cost.
Landfill & Debris Removal
Disposing of debris is a significant part of the demolition process. Landfill tipping fees and transportation costs may account for 20-30% of the total project cost. Recycling some materials, like concrete or metal, can offset these expenses.
Asset Recovery and Recycling
Some demolition projects incorporate asset recovery, salvaging valuable materials like copper wiring, steel beams, or wood paneling for resale or reuse. While this can reduce costs, it requires careful coordination and time and slightly increases labor expenses upfront.
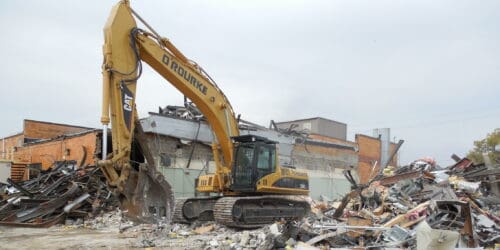
How to Find the Right Commercial Demolition Contractor
Finding the right commercial demolition contractor is critical for the success and safety of your project. Start by researching contractors with extensive commercial demolition experience, particularly in similar projects. Look for companies with strong safety records, proper licensing, and certifications that adhere to industry standards. It’s also important to verify the contractor’s expertise in handling environmental remediation, especially if your project involves hazardous materials like asbestos or lead.
Get an Accurate Estimate for Your Commercial Demolition Project
Start by seeking estimates from reputable contractors with experience in commercial demolition. A thorough estimate should include:
- Detailed breakdowns of costs for labor, equipment, permits, and debris removal.
- An assessment of potential environmental remediation needs.
- Timelines for project completion.
Ask for references and review the contractor’s safety record and compliance with local regulations to ensure you’re working with a trustworthy team.
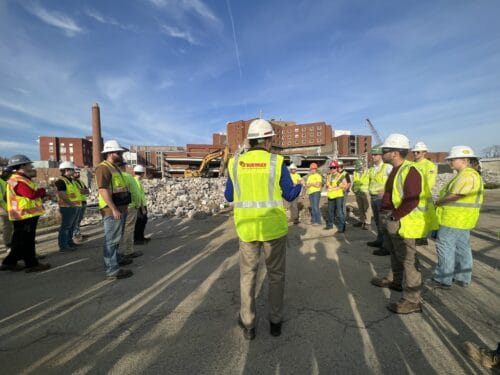
Frequently Asked Questions
What are the most common methods of demolishing a commercial building?
The most common methods include implosion, where explosives are used to bring the building down, mechanical demolition, using heavy machinery like excavators, and selective demolition, which focuses on preserving reusable materials. The choice depends on the building’s structure and surrounding area.
Are there any tax incentives for demolishing a commercial property?
Yes, some municipalities and states offer tax incentives or grants for demolition projects that aim to improve urban spaces or promote redevelopment. Additionally, recycling salvaged materials may qualify for tax deductions.
What safety measures should be taken when demolishing a commercial building?
Safety measures include thorough site inspections, adherence to OSHA regulations, proper use of personal protective equipment (PPE), and ensuring trained professionals handle hazardous materials. Regular safety audits are essential to avoid accidents and ensure compliance.
Final Thoughts About Commercial Demo Costs
Understanding the various factors and costs associated with commercial demolition helps ensure a smoother project experience. Partnering with an experienced demolition contractor, like O’ROURKE Wrecking Company, can provide the expertise and reliability you need for your next project.
When it comes to the precise and efficient removal of old, damaged, or unused silos, O’ROURKE Wrecking Company stands as the trusted industry leader. We combine decades of expertise with advanced techniques to deliver safe, cost-effective solutions tailored to your specific needs. Whether you require the dismantling of towering industrial silos or smaller agricultural ones, our team ensures every project is completed safely and efficiently.
Learn more about our silo demolition solutions from this news story about the Beekman Grain Silos that O’ROURKE demolished in Cincinnati
Expert Silo Demo You Can Trust
At O’ROURKE Wrecking Company, we pride ourselves on delivering expert silo demolition services that prioritize safety, precision, and customer satisfaction. Whether dealing with agricultural, industrial, or storage silos, our skilled team ensures a seamless process from start to finish.
Safe Removal & Recycling of All Types of Old, Damaged, or Unused Silos
Removing a silo is a complex task that demands expertise to avoid risks to property and personnel. Our skilled professionals are trained to handle the safe dismantling of all silo types while adhering to industry safety standards. We specialize in safely dismantling and removing silos of all types, including concrete, steel, and composite structures. Our commitment to sustainability means we prioritize recycling materials whenever possible, minimizing waste and maximizing resource reuse.
Our Demolition Process
Our comprehensive demolition process is designed to streamline operations, ensuring a seamless experience from start to finish.
Initial Consultation and Site Assessment:
Our experts assess the silo and its surroundings to identify potential challenges and determine the best approach.
Custom Demolition Plan:
Every silo is different, and we develop a tailored plan that incorporates advanced technology, safety protocols, and client requirements.
Permitting and Compliance:
O’ROURKE Wrecking Company ensures all permits and environmental regulations are in place before beginning any project.
Safe Demolition Execution:
Using specialized equipment, our team systematically dismantles the silo, carefully managing debris and minimizing risks.
Material Recycling and Site Cleanup:
After the demolition, we recycle salvaged materials and leave the site clean, ready for future use.
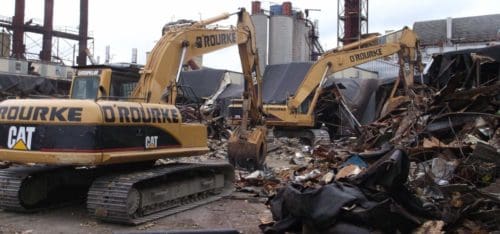
Frequently Asked Questions
What is Silo Demolition?
Silo demolition involves the safe dismantling and removal of silos that are no longer functional or needed. This process may include breaking down concrete walls, cutting through steel frames, and clearing the site of debris to prepare it for future use.
Why Would a Silo Need to Be Demolished?
There are several reasons for silo demolition, including:
- Structural damage from age, weather, or wear.
- Lack of use or changing operational needs.
- Safety hazards posed by unstable or deteriorating silos.
- Redevelopment plans for the property where the silo is located.
How Much Does Silo Demolition Cost?
The cost of silo demolition varies depending on factors such as the size and material of the silo, its location, accessibility, and whether hazardous materials like asbestos are present. Contact O’ROURKE Wrecking Company for a customized quote.
What Are the Different Types of Silos?
Common types of silos include:
- Concrete Silos: Typically used in agriculture for grain storage.
- Steel Silos: Popular in industrial applications for material storage.
- Tower Silos: Tall, cylindrical structures often seen on farms.
- Bag Silos: Flexible and portable storage options.

Why Choose O’ROURKE Wrecking Company for Silo Demolition?
O’ROURKE Wrecking Company combines decades of experience with cutting-edge technology to deliver superior silo demolition services. Here’s why clients trust us:
- Safety First: Our team prioritizes safety, ensuring every project adheres to strict protocols.
- Environmental Responsibility: We emphasize recycling and waste reduction to protect the environment.
- Expertise Across Industries: From agricultural to industrial silos, we have the knowledge and tools to handle any challenge.
- Customer Satisfaction: We work closely with clients to ensure their needs are met every step of the way.
Let O’ROURKE Wrecking Company handle your silo demolition needs with professionalism and efficiency. Contact us today to get started!
When it’s time to demolish a parking structure, you need a demolition partner with the skills, experience, and precision to get the job done efficiently and safely. At O’ROURKE, we specialize in parking structure demolition for multi-level parking decks and garages. Our team ensures each step is carefully executed, minimizing disruptions and safeguarding surrounding areas.
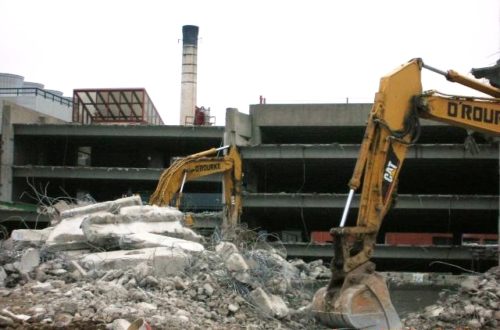
Why Parking Structure Demolition is Necessary
Over time, parking garages can become unsafe due to structural degradation and concrete deterioration. In other cases, urban developments and zoning changes may require the removal of old structures to make way for new, modern projects. Regardless of the reason, demolishing a parking structure is a complex task that requires detailed planning, specialized equipment, and expert management.
Some common reasons to demolish a parking structure include:
- Structural instability due to aging materials
- Design flaws that no longer meet safety codes
- Reconstruction or expansion of urban developments
- Repurposing the area for commercial or residential spaces
- Removal of environmental hazards, such as mold or asbestos
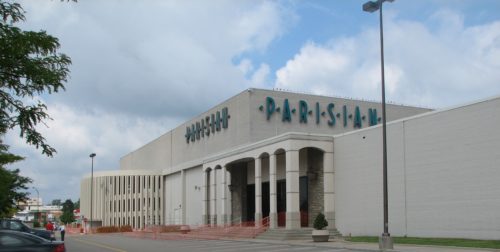
O’ROURKE’s Approach to Parking Structure Demolition
At O’ROURKE, we understand the unique challenges involved in demolishing parking structures. Our demolition process is guided by safety, precision, and environmental responsibility, ensuring that every project is handled with care. Below is an overview of our approach.
Planning and Permitting
Every project begins with a thorough site assessment. We work closely with your project managers, engineers, and local authorities to obtain the necessary permits and develop a demolition plan tailored to the structure’s size, materials, and location. Our team identifies hazards early, such as asbestos, and ensures compliance with regulations.
Selective and Controlled Demolition
Parking garages are often located in busy urban areas, which makes safety a top priority. We use fencing, signage, and traffic control plans to ensure the safety of the public and surrounding property. Our teams work efficiently to minimize disruptions to nearby businesses and residents. Whether we’re dismantling a multi-level parking deck or a smaller structure, precision matters. We employ techniques like:
- Selective demolition to preserve surrounding buildings and infrastructure
- Controlled implosions for larger parking structures, ensuring a safe collapse
- Use of heavy machinery for concrete breaking and steel removal
Debris Management and Recycling
Concrete, steel, and other building materials from the demolition site are processed to maximize recycling. This not only reduces waste but also ensures environmentally responsible practices. We coordinate with recycling facilities to dispose of materials in compliance with local laws. If there are hazardous materials, such as lead, asbestos, or mold, our licensed abatement team will remove the hazardous materials in accordance with state and federal regulations.
Timely Completion and Site Preparation
We understand that projects often have tight timelines, especially when new developments are planned. Our experienced team ensures the job is completed on schedule, and we offer site preparation services to make the space ready for the next phase of construction.
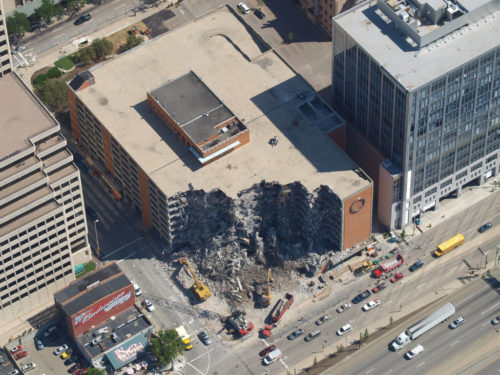
Benefits of Choosing O’ROURKE for Parking Structure Demolition
When it comes to demolishing parking garages, you need a contractor who understands the nuances of structural demolition, environmental safety, and urban planning. O’ROURKE brings all these elements together, ensuring that each project is executed flawlessly. When working with O’ROURKE, clients receive more than just demolition services; they gain a partner committed to the project’s success.
- Experience & Expertise: With years of experience, O’ROURKE has handled complex parking demolition projects across industries.
- On-Time and Within Budget: Our project management ensures deadlines are met, and costs are controlled.
- Safety First: We prioritize worker and community safety with rigorous protocols and certified professionals.
- Sustainable Practices: Our recycling efforts reflect a commitment to environmental responsibility.
- Specialized Equipment: From concrete crushers to high-reach excavators, we bring the right tools to every job.
Contact Us Today To Get Started On Your Demolition Project
Whether it’s a small underground parking lot or a multi-story garage, O’ROURKE has the skills, tools, and expertise to complete the job efficiently. Ready to get started on your demolition project? Contact us today for a consultation – our team will work with you to assess your property’s needs and develop a tailored solution that works for you.
By choosing O’ROURKE, you’re partnering with a trusted demolition expert who can manage the challenges of parking structure demolition while minimizing disruptions and environmental impact. Interested in learning more about our past demolition work for parking properties? Check out our past projects to see some examples of our top-rated demolition solutions.
When hospitals and healthcare facilities reach the end of their lifecycle, it’s critical to rely on an experienced demolition team to handle the delicate process of deconstruction. O’ROURKE’s hospital demolition services ensure these projects are carried out safely, efficiently, and with minimal environmental impact. Here’s a closer look at how our team navigates the complexities of hospital demolition.
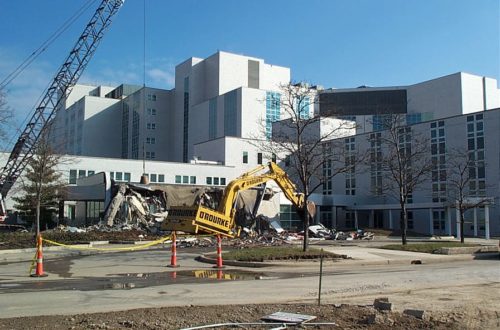
Why Hospitals Require Specialized Demolition Services
Demolishing healthcare facilities is not as simple as tearing down walls and removing debris. These structures often contain specialized equipment, hazardous materials, and unique layouts that require expert handling. Key challenges in hospital demolition include:
- Asbestos and Lead Removal: Older hospitals may contain asbestos insulation and lead-based paint, which must be carefully removed to avoid contamination.
- Medical Waste Management: Safe disposal of biohazards or leftover medical waste is critical to comply with health regulations.
- Environmental Concerns: Safeguarding air and water quality during demolition is essential to protect nearby communities.
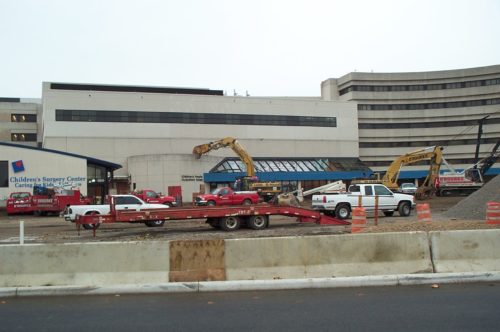
The O’ROURKE Approach to Hospital Demolition
At O’ROURKE, we take a meticulous approach to hospital demolition to ensure that every step is executed with precision and care. Our process typically includes:
1. Pre-Demolition Planning and Assessment
We begin each project with a thorough inspection of the facility. This includes identifying any hazardous materials, mapping out utility disconnections, and developing a customized demolition plan that minimizes disruption.
2. Selective Demolition for Asset Recovery
Whenever possible, O’ROURKE salvages reusable materials such as medical equipment, metal, and electrical components. Selective demolition not only reduces waste but also contributes to sustainability efforts.
3. Asbestos and Hazardous Material Abatement
Our certified team is trained to safely remove and dispose of asbestos, lead, and any hazardous medical materials in accordance with state and federal regulations.
4. Dust and Noise Control
Hospital demolition projects are often located near operational healthcare facilities or active commercial and residential areas. O’ROURKE implements dust suppression techniques and noise-reduction strategies to minimize the impact on surrounding communities.
5. Debris Removal and Site Cleanup
Once the structure is deconstructed, our team handles the efficient removal of debris, ensuring the site is clean and ready for redevelopment or new construction.
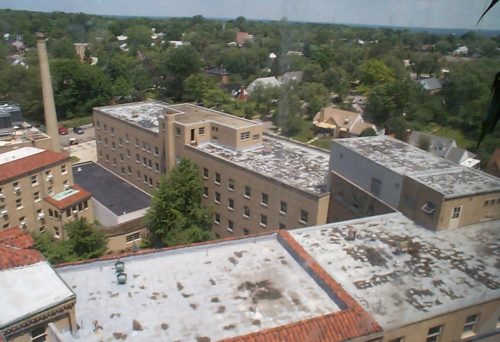
Why Choose O’ROURKE for Hospital Demolition
At O’ROURKE, we understand the complexities of hospital demolition and offer tailored solutions that align with your project’s goals. Here’s why clients trust us:
- Industry Expertise: With years of experience in the demolition industry, we have successfully completed projects for dozens of hospitals, clinics, and medical facilities.
- Regulatory Compliance: We stay updated on the latest regulations to ensure your project meets all legal requirements.
- Commitment to Safety: Our safety-first approach ensures a smooth and accident-free demolition process.
- Customized Solutions: Each hospital project is unique, and we create demolition plans that meet the specific needs of your facility.
Compliance and Safety: Our Top Priorities
Healthcare demolitions demand a high level of compliance with safety standards. O’ROURKE’s demolition specialists adhere to OSHA guidelines, EPA regulations, and healthcare-specific protocols to ensure each project meets the required standards.
Our focus on safety includes:
- Comprehensive Risk Assessments
- Ongoing Safety Training for Crews
- Proper PPE and Equipment Handling
- Strict Compliance with Waste Disposal Regulations
Check Out Our Past Projects
Ready to get started on your medical facility or hospital demolition project? Contact us today for a consultation – our team will work with you to assess your property’s needs and develop a tailored solution that works for you. By choosing O’ROURKE, you’re partnering with a trusted demolition expert who can manage the challenges of hospital demolition while minimizing disruptions and environmental impact. Interested in learning more about our past demolition work for hospitals? Check out our past projects to see some examples of our top-rated demolition solutions.